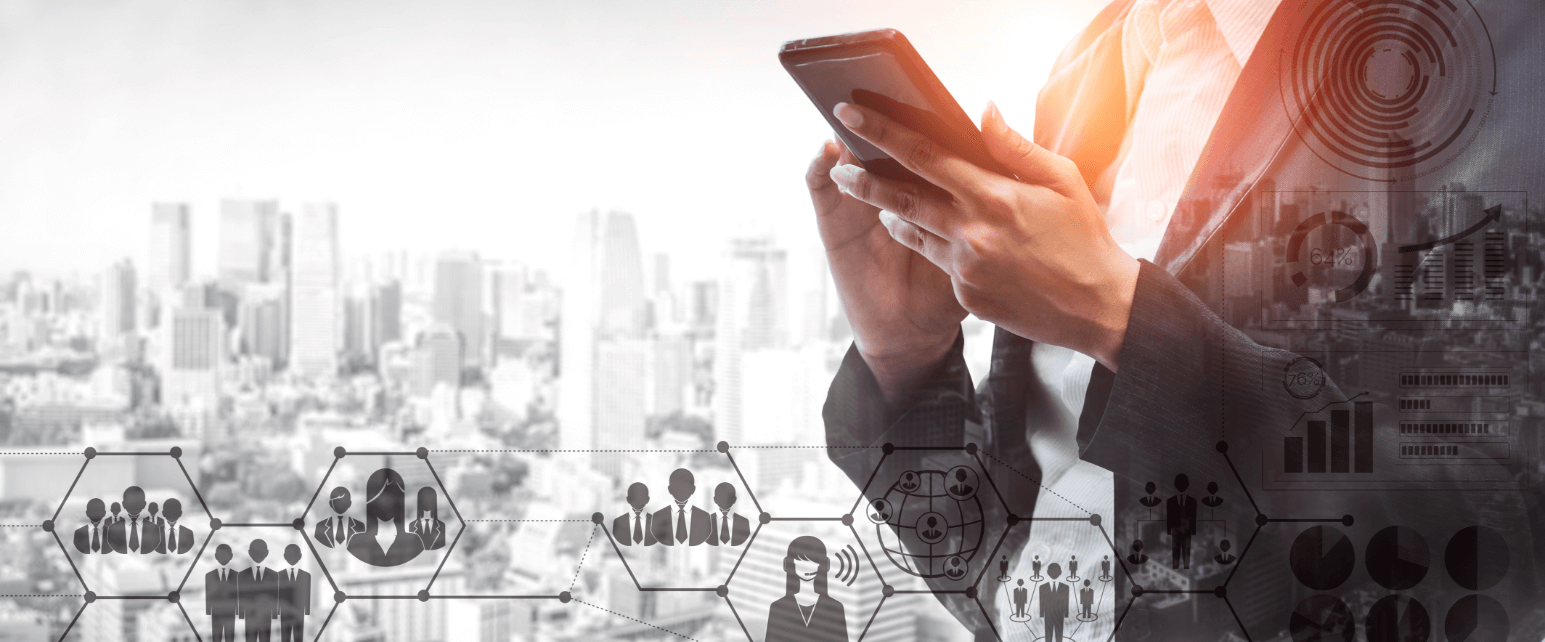
OUR ACTIVITIES
Any international inspection company is welcome to inspect our premises.
We can create any sample and produce according to the Buyer’s requirements. We value prompt and efficient deliveries. International A.Q.L is maintained for products of standard quality.
We need to receive the order sheet from the Buyer to start production as soon as possible.
- L/C or T/T
- Colour swatch
- Size spec/measurement chart
- Order sheet/size break down
- Accessories/trims details
- Print/embroidery details (If any)
- Packing method/instruction
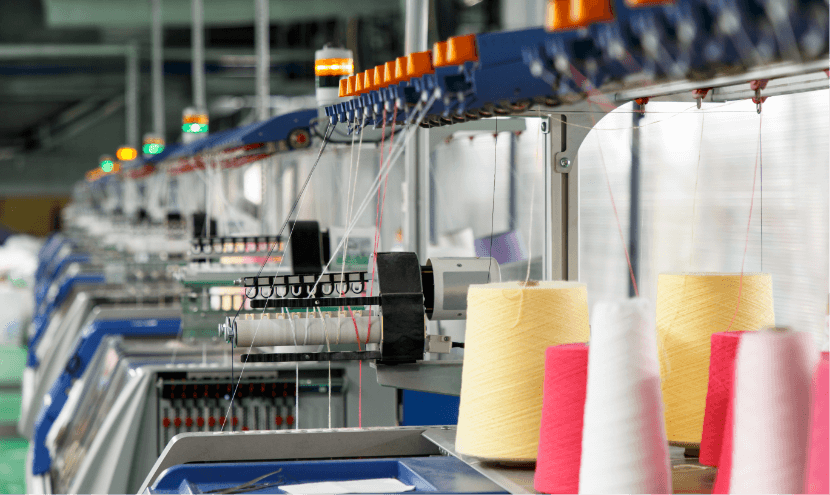
Apparel Merchandiser: Pre-production Activities
Before going to the production, there are some essential activities that the garment merchandiser should perform. These are listed below:
- Tech pack received from the buyer
- Product approval from the buyer
- Product development
- Order confirmation
- Pricing
- Fabric and accessories consumption
- Fabric and accessories booking
- Fabric and accessories in-housed
- Going to the production
Below are the activities of the finishing department
A finishing department’s main activities include thread trimming, checking garments, and ironing. In the finishing department, the packing section handles the folding, tagging, and packing of garments. This article will cover the main functions of the finishing department. These functions can change as product categories change.
- Checking garments
- Thread Trimming
- Removing stains
- Ironing garments
- Going to the production
- Button attach and Butting holing
- Repair work and mending
- Fabric and accessories consumption
- Fabric and accessories booking
- Fabric and accessories in-house
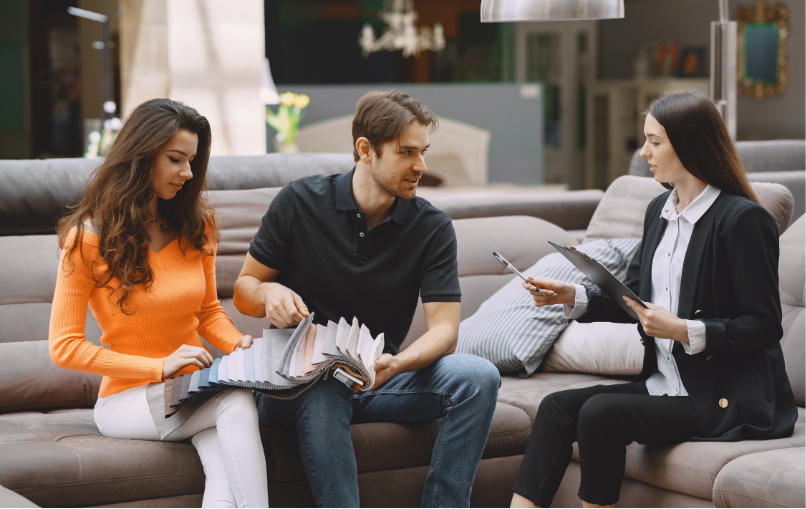
Our Responsibilities
The buyer will receive the Styling Samples and Lab Dip along with the fabrics. This allows the buyer to approve the Styling and Lab dip. We receive the buyer’s comments regarding the Styling Approval, Lab dip, and the workable L/C/T before sending the Pre-production samples and accessories card to the buyer for approval. Our quality control teams conduct daily inspections and prepare reports. Then we send the report to the buyer. Once production is complete, our quality control team performs the final inspection before shipping, and we notify the buyer if there are any changes.